Balance of Plant
From Burner Management to Plant Control
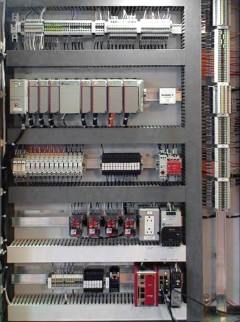
Balance of plant is a general term referring to the control of ancillary equipment surrounding the boiler, dryer, or heater. Examples of the ancillary equipment that we control are the deaerator, the surge tank, the condensate storage tank, the hot well, water softeners, air handling units, fans, pumps, etc.
The balance of plant system can be controlled by a single panel or multiple panels distributed throughout the plant. The system can be comprised of a central panel containing the primary logic solver and/or local panels at each piece of equipment. The local panels can be simply an I/O module (such as Point IO) controlled from a central PLC or it can be an independent PLC panel with a dedicated HMI.
Balance of Plant Control
We offer the following core functionality in our systems:
- Boiler plant master firing rate control modulates the boilers in unison, or it can base load boilers at the load where they obtain peak efficiency.
- Standby boilers are kept warm via shell temperature control. When the shell temperature drops, the standby (lag) boiler will start and hold at low fire until the temperature is satisfied and then turn off. This facilitates the lead-lag sequencer so that the lag boilers are warm and ready.
- Equipment lead-lag sequencer automatically starts the optimal number of boilers, pumps, or fans for the plant load (hereafter referred to as unit). The lead-lag sequence can simply alternate the lead on each cycle, run a custom sequence for lead and lag, transfer leads in a circular rotation, or automatically select lead based on the accumulated runtime hours. This sequencer will call for the next device should the quantity running not be able to keep up with the load or if a unit fails. Should a unit in the sequence not be available, it will be ignored and the next in the sequence will start immediately in its place. When the failed or otherwise unavailable unit becomes available, it will then take its place in the sequence only after it has run long enough to be effective. Only at that time will its substitute be turned off.
- Tank level control is accomplished by monitoring the actual level in the tank and modulating a makeup valve or VFD pump speed. Most tanks in the power house have multiple feeds with each having their own control loop.
- Feedwater pressure control is important for maintaining the proper water level in watertube boilers. A consistent pressure will permit the feedwater valves to operate at their design flow coefficient. We recommend controlling the feedwater pressure using a differential pressure transmitter for a consistent pressure drop between the feedwater header and steam header, aiding the effectiveness of the control valve.
- Air handling unit control is important for maintaining sufficient air flow into a boiler room. We can automatically sequence the air handlers and control face & bypass dampers to regulate air flow and temperature into the boiler room.

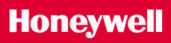
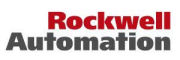
Call 603-764-5547 or email us today
to see how our experts can help.