Combustion Control Systems
Combustion control systems are used in many industrial applications. We have experience implementing combustion control strategies on firetube and watertube boilers, waste steam superheaters, air pre-heaters, once through steam generators, duct burners, incinerators, fluidizing bed dryers, rotary dryers, and the list goes on. The market that we serve is for burners with an input range from 20-500 mmbtu/hr.
Combustion Control
We offer the following core functionality in our systems:
- Master firing rate control modulates the burner to maintain a constant outlet pressure or temperature. A selection is provided so that the firing rate can be driven by either a local control loop or a plant master control signal.
- Single point positioning (jackshaft) control physically links the fuel and air together with a mechanical linkage. This control strategy is typically used on burners under 20 mmbtu/hr input. Combustion adjustments should be conducted twice a year on this type of system.
- Parallel positioning control electronically links the fuel and air together using cross-limiting logic. Each valve and damper has its own dedicated servo. The control system monitors the servo position feedback so that it has positive confirmation of the servo position and a safety shutdown will be initiated on a position error. This control strategy is typically used on burners under 60 mmbtu/hr input. When coupled with oxygen trim this system can operate for a year or more before needing adjustments to the combustion.
- Full metering control is similar to parallel positioning since there is no linkage and each valve and damper has its own dedicated servo. However, instead of using servo position feedback monitoring, the full metering control monitors the actual fuel flow and air flow. Full metering control can provide tighter, more efficient combustion because it automatically adjusts for changes in fuel pressure and ambient conditions. Provided that quality flow meters are used and oxygen trim is implemented, this control system can operate for several years before needing adjustments to the combustion.
- Oxygen trim control monitors the oxygen content of the flue gas and trims the air so that the set point as defined at the time of tuning can be maintained.
- Draft control is used when the stack is over 50' tall or if there is an induced draft (ID) fan. Package boilers typically operate at 0"wc at the boiler outlet, brick set boilers typically operate at -0.2"wc in the furnace. We can modulate the ID fan VFD and/or ID damper to maintain draft
- Flue gas recirculation (FGR) is used to reduce NOx emissions. We can control this by positioning, flow, or by adjusting fresh air intake. We also offer windbox oxygen trim for fine-tuning the FGR where tighter control is required.
- Water level control can be 1, 2, or 3 element. The first element is water level, second is steam flow, and the third is feedwater flow. This control features the ability to predict the volume of water required before the change is even shown in the water column.

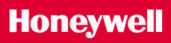
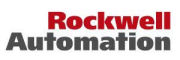
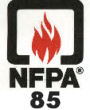
Call 603-764-5547 or email us today
to see how our experts can help.