Photo Gallery
Plant Master Control and SCADA: VA Medical Center
Here is a Plant Master Control Panel and SCADA system we built for a VA medical. Chuck completed the start-up a couple of weeks ago. The system is designed to control three boilers, a deaerator tank level, a surge tank level, boiler feedwater pumps, and condensate transfer pumps.
Boiler Control Panel: Dairy Industry
Got Milk? Here is a panel that we constructed for the dairy industry. The System uses a Fireye flame safeguard for burner management. The combustion control system is a CompactLogix system capable of dual fuel firing on natural gas and biogas.
Dowtherm Heater: Lumber Treatment Plant
We did this project a few years ago. We used a single enclosure with two identical dowtherm heater systems. The original system used TRIAC control for the fuel valves. Recently the end user wanted to change the old TRIAC valves with new valves controlled by a 4-20mA signal. We designed an insert plate to go into the existing fully wired panel so they can install the new side panel and plug the new ControlLogix cards into the chassis.
Constant Flow Heater Control Panel: U.S.A
This Constant Flow Heater Control Panel is designed to keep a selected boiler in a three-boiler system on hot standby using steam-heated water constantly circulating through the boiler.
If a boiler is selected to be the standby boiler, and the supply temperature is below setpoint, the inlet and outlet valves to the boiler will open, and the circulation pump will start. If the supply temperature remains below the setpoint for a set time, the steam control valve will open up and introduce steam to the boiler's feedwater inlet. Once the supply temperature reaches the set point, the steam control valve will modulate as required to maintain the correct temperature. This system was used as an alternative to installing an aquastat or mud drum steam coil system.
Boiler Sequencing Control Panel: Bakery
Boiler Sequencing Control Panel for a bakery in New York
Boiler Control Panel: Power Plant
This is a project we did for a natural gas-fired electric generation facility. The facility produces 1,100-megawatts of electricity.
The panel was designed for a hazardous location, and sports a 22" Hope Industrial Systems monitor, running FactoryTalk view studio site edition on an Allen-Bradley industrial PC. Using ControlLogix PLC for combustion control, and Fireye for burner management.
Boiler Control Panel: Power Plant
BMS/CCS control panel we designed, fabricated, and programmed to assist in the start-up of a natural gas power plant.
Fun fact about the boiler we are controlling, some of its steam is used in a snow melt system that keeps 10 acres of roads and sidewalks clear!
Pump Sequencing Control Panel: Hospital
This system provides fuel for two day tanks. The control system will start and stop pumps based on the level of fuel in each of the day tanks.
The float switches in the Day Tank send a signal to the control panel. When either of the day tank levels drops, the system starts a pump and opens the solenoid valve to refill the day tank. Each pump has a Hand/Off/Auto switch allowing for manual or automatic control of the pumps.
Plant Master: Furniture Manufacturing
This panel controls a wood-fired boiler system, it has seven 3-phase 480v motors, three of which are controlled by VFD's.
HTHW Heater: Correctional Facility
This system provides the flame safety control for a industrial high temp hot water generator (HTHWG).
The BMS is interfaced with a series of limit switches, flame detection, motor starters, solenoids, transformers, and safety shutoff valves.
The combustion control system has been designed for firing rate control of a burner using a full metering combustion control system.
Well Pump Controls: Public Water System
Well Pump Controls, consisting of a Pump House Panel and Storage Tank Panel tied together through wireless communication. The Pump House Panel controls seven pumps, turning on and off working together to fill a 100,000 gallon water tank. While the Storage Tank Panel controls three VFD pumps in a lead-lag sequence to maintain water pressure in the main waterlines.
Boiler Control and Balance of Plant: University
Four boiler control panels are set up for dual fuel, fully metered combustion control, and 3-element feedwater. The Balance of Plant panel controls the boiler & pump lead/lag sequencing, steam header pressure, and tank level controls. All five panels with Allen-Bradley 5380 CompactLogix controllers and a pair of redundant SCADA computers to keep all the historical data.
4 total photos
Mobile Boiler Room Panel
Our guys here at Stanyan Hill built this panel for a 1000HP Mobile Boiler Room.
Mobile boiler rooms are great solution for planned/unplanned downtime, project delays or natural disasters.
This panel controls all functions of the boiler room, even the boiler rooms own heating and ventilation.
Built rugged, packed into a 53ft trailer.
BMS Control Panels: Refinery
Two identical, Class 1 Division 2, UL hazardous location listed BMS control panels, we built, programmed and tested.
Plant Master, Feedwater and BMS/CCS Boiler Control Panels: Medical Center
Plant Master, Feedwater, and three identical BMS/CCS Boiler control panels
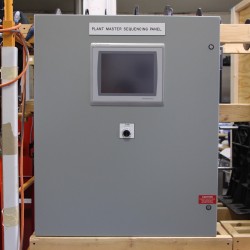
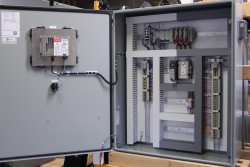

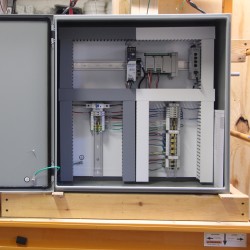
6 total photos
Boiler Control: University
One of two identical BMS/CCS control panels. Helping to reduce (NOx), each unit controls an SCR(Selective catalytic reduction) system. A Built-in air conditioning unit keeps the redundant PLCs cool, and a HUGE 19” Allen Bradley PanelView Plus HMI touch screen keeps vital information at your fingertips.
4 total photos
BMS/CCS Boiler Control Panel: Japan
This system provides flame safety and combustion control for the duct burner in a HRSG (Heat Recovery Steam Generator). The HRSG is fed exhaust gases from four generators.
Balance of Plant: Correctional Facility
Here's one of our Balance of Plant Systems that was sent out to a correctional facility. The system is currently providing flawless control to the following systems:
- Three boiler lead/lag sequencing and firing rate control.
- Five boiler feed pump lead/lag sequencing and speed control.
- Condensate tank level control.
- Deaerator tank level control.
- Heat exchanger temperature control.
- Air handling flow and temperature control (intake and exhaust fans).
Any plant, big or small, can benefit from a Stanyan Hill Controls Balance of Plant system.
SCADA: University
Built with powerful Dell Hardware and programmed with Rockwell Automation FactoryTalk Software, our SCADA systems deliver more than just robust control and insightful monitoring - they deliver peace of mind. This unit went out to a university that is also equipped with four of our boiler control panels and one of our plant master control panels.
This SCADA will be interfacing with a deaerator tank, a surge tank, three boiler feed pumps, two condensate transfer pumps, four boilers, and several control valves, providing the operators with historical trending and powerful alarm functionality.
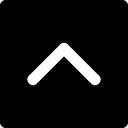