Burner Management
Burner management systems are used in conjunction with the combustion control. Burner management is the safety system insuring that it is safe to have a flame in the furnace.
Should a situation arise where it is no longer safe to run then this system will initiate a shutdown and prevent fuel from entering the furnace. In addition to supervising the safety of the fired equipment, this system will also sequence the burner through the firing cycle.
The following are typical steps that are required:
- Standby
- Start fans
- Drive to purge
- Pre-purging the flue passages
- Drive to low fire light off
- Trial for ignition
- Main flame trial
- Release to modulate
- Post-purging the flue passages
- Stop fans
Burner Management Control
We offer the following core functionality in our systems:
- Microprocessor flame safety controls such as those manufactured by Fireye and Honeywell, are cost-effective solutions for single burner or unison fired burners. We frequently incorporate these controls into our burner management systems. The flame safety control is the primary component; however, to complete the system several selector switches and relays are required.
- General purpose PLCs (SIL 0-2) comprise many of our burner management systems. Since the majority of our systems are controlling burners on industrial watertube boilers, we closely follow and adhere to NFPA 85. The NFPA has strict rules regarding the implementation of a general purpose PLC so that inputs and outputs are verified to be functioning properly and are not stuck on or off. Also, an external watchdog timer is used to verify that the CPU is working correctly. Lastly, a master fuel trip will not permit fuel if there is any failure in the system to enter through the burner.
- Safety PLCs (SIL 3) are similar to that of the general purpose PLCs except that the I/O checking is inherent in the I/O cards. Also, instead of using an external watchdog timer to check the CPU, a safety PLC will have a primary processor and a safety partner. Both the primary processor and safety partner must be operating properly or the burner will shutdown to a safe state. The primary benefit of the safety PLC over the general purpose PLC in a burner management application is that it has a much higher mean time between failure (MTBF), for minimal downtime since the PLC components are tested to a higher standard.
- PLCs offer the following benefits over the microprocessor flame safety controls: advanced diagnostics, complex custom logic via code rather than hardwiring through relays, simple implementation of on-the-fly fuel changeover, multi-fuel simultaneous firing, and multiple burner sequencing & control.

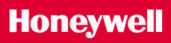
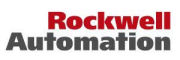
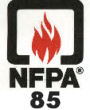
Call 603-764-5547 or email us today
to see how our experts can help.